ROCKWOOD celebrates delivering 2,500th part to Roxel with new contract award! Click Here to read the full article.
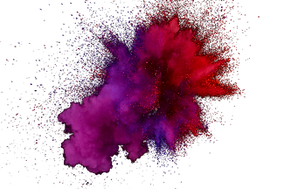

25 years of supplying the aerospace, defence and nuclear industries with a proven track record of delivering complex structures.
​
Compression and Bladder moulding
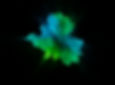
Specialising in compression and bladder moulding of pre-preg composite material in metal tooling, we have taken component manufacture to the next level. The processes allow an extraordinary variety of parts to be made with levels of complexity that other method would find hard to match.
​
Metal tooling allows very fine and complex detail to be imparted in the tooling. For instance undercuts, collapsing cores, side actions and interchangeable inserts can all be incorporated in multi-functional tooling. Additionally, compression moulding and bladder moulding can take place in a single tool within a single moulding operation, which has the ability to reduce part count and cost.
​
Metal tooling also allows for a higher degree of design freedom than you would have with autoclave, vacuum bag or pressure bag processes in composite tooling. The only limitation with metal tooling relates to larger parts where tool size and weight prevent simple manhandling operations.
​
Despite some entrenched misconceptions, metal tooling is not an expensive option. Typically CAD models of parts are scaled appropriately to compensate for thermal contraction of the component and tooling. The tool component pieces are then CNC machined straight from CAD models. There are no intermediate steps. Tool components are hand polished, sealed, released and ready for manufacture. The tool process cycle is fast, resulting in production ready tooling. The secret to the manufacture of metal tooling is simply ‘lights-out’ engineering.
​
Compression and bladder moulding in metal tooling allows engineers and designers the freedom to innovate. Please call for further information.

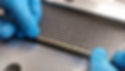

Our broad based in-house design and engineering capability to provide innovative products and product manufacturing solutions.
​
Manufacturing processes and expertise that are not frequently found in the UK composites industry.
​
Short lead times from concept to hardware, through in-house design, tool manufacture and development.
​
Rapid problem solving and customer support backed by ISO 9001:2015 manufacturing systems.
​
We have a proven track record of producing high quality products and the ability to deliver components on time.
​
We are happy to discuss and support design engineers in the selection of appropriate component materials, tooling and production systems.
​
"Design for Manufacture" is key in minimising tooling cost, maximising quality and reducing component cost and lead time. Please call to discuss.
What differentiates Rockwood Composites?
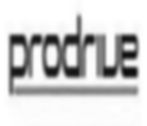

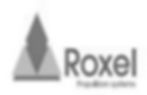


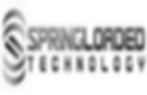

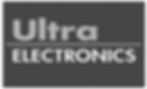



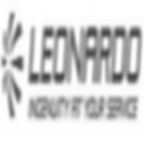

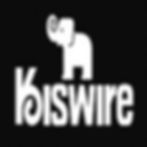
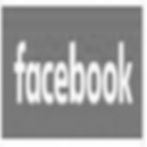

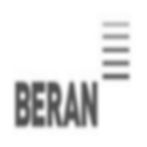

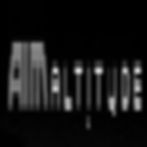

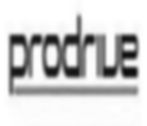

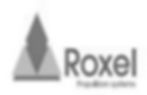


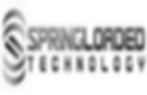

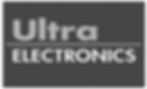



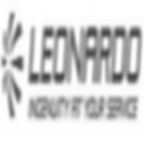

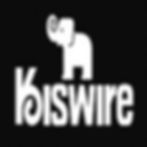
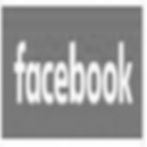

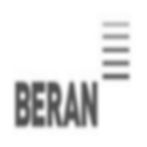

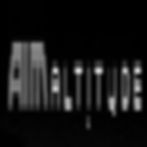

Clients list